1. Product introduction
The HonorPrint M series metal powder melting rapid prototyping system is composed of: laser, galvanometer scanning system, host forming room, powder feeding mechanism, dust removal device, control system, computer and 3D printing special software. The schematic diagram of the HonorPrint M series forming process is shown in Figure 1. During the forming process, in order to prevent the metal powder material from being oxidized, the forming cavity should be sealed and filled with protective gas. When forming, first spread a layer of powder material on the workbench with a scraper. Then, under the control of special software for 3D printing, the laser beam scans the solid part of the powder based on the cross-sectional profile information to raise the temperature of the powder to the melting point. Above, the scanned powder melts and then drops below the melting point, bonding to each other to form a sintered surface. The powder in the non-scanned area is still loose and serves as a support for the workpiece and the next layer of powder. After the forming of one layer is completed, the workbench is lowered by the height of one layer, and then the next layer is laid and formed. This cycle continues to form a three-dimensional workpiece.
2. Technical parameters
project | name | HonorPrint M300 |
parameter | forming space | 300×300×350mm |
molding material | Stainless steel, cobalt-chromium alloy, titanium alloy, high-temperature nickel-based alloy, aluminum alloy and other metal powder materials |
Part accuracy | ±0.1mm (L≤100mm) or ±0.1% (L>100mm) |
Layer thickness | 0.02~0.05mm continuously adjustable |
protective gas | Nitrogen or argon |
Hardware specifications | laser | Fiber laser, power 500W, wavelength 1060nm~1080nm |
Scan system | High-speed and high-precision galvanometer, dynamic focus scanning system; focal plane spot size: ≤0.1mm; *** scanning speed: 8m/s, scanner repeat positioning accuracy ≤0.01mm, zero drift automatic correction. |
Optical system | QBH collimating lens |
visual system | Can monitor printing and molding quality during the part making process |
Powder spreading system | Flexible scraper for powder spreading |
Industrial computer | Industrial computer, mainstream configuration |
laser cooler | Fully enclosed constant temperature circulation water cooling, cooling capacity 2.5kW; rated power 1.5kW |
security measures | Automatic shutdown function, automatic shutdown when malfunction occurs, laser safety protection |
Software work platform | Windows 11 | * Automatic slicing software system: the control software can directly read STL files * Visualization of STL files, with graphics transformation functions such as rotation, translation, zooming * STL file fault-tolerant slicing technology, no need for additional error correction software and manual error correction, partitioning Direction-changing scanning * Real-time dynamic simulation of prototyping * Lifetime free software upgrades |
working environment | Voltage | 3-phase 5-wire, 380V±10% |
frequency | 50Hz±2% |
ambient temperature | 18~25℃ |
relative humidity | less than 60% |
3. Application cases

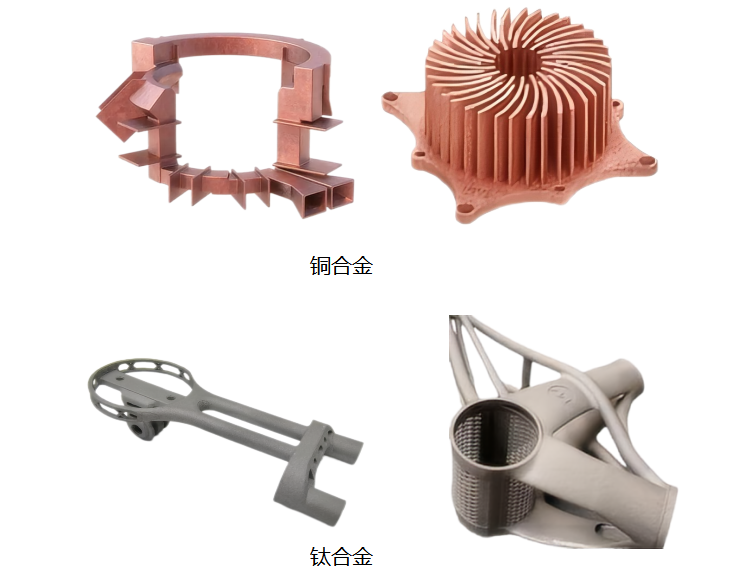