1. Equipment principle
The large-table complex SIC ceramic laser powder bed fusion 3D printing system has a multi-laser, multi-galvanometer scanning system and is equipped with massive data processing software, which solves the problem of multi-laser galvanometer collaborative work, massive data processing, in-situ forming of green blanks, and powder cleaning. , post-curing treatment and other problems to achieve the integrated forming of large and complex ceramic components. Its maximum forming size reaches 1700 mm×1700 mm×600 mm.
Schematic diagram of laser powder bed fusion 3D printing equipment for large complex ceramic components: 11-laser, 12-galvanometer, 13-insulation layer, 14-heating device, 15-powder spreading scraper, 16-powder spreading cylinder, 17-forming cylinder , 18-forming cylinder wall, 19-forming blank, 110-forming table, 111-forming cylinder wall lifting device, 112-SLS equipment lifting device, 113-guide wheel, 6-guide rail, 115-ground
Large-scale ceramic laser powder bed fusion equipment developed: (a) Overall view of the 1.7 m equipment; (b, c) Scanning using four lasers and four galvanometers; (d) Bucket-type two-way powder spreading; (e) Multi-scanning system segmentation and splicing software
2. Post-processing process of selective laser sintering ceramic parts
The ceramic part formed by selective laser sintering is just a green body, and its mechanical and thermal properties usually cannot meet the requirements of practical applications, so it must be post-processed. According to the requirements of the final product, the commonly used post-processing process is generally the preparation of reaction sintering silicon carbide.
3. Product performance parameters
project | name | Honor3d C500 technical indicators and specifications |
parameter | forming space | 500mm×500mm×400mm |
Forming materials | Silicon carbide, alumina, zirconia and other ceramic materials |
Part accuracy | The size is less than 100mm, and the forming size deviation is less than 0.5mm; The size is greater than 100mm, and the forming size deviation is less than 1% |
Layer thickness | 0.08~0.3mm continuously adjustable |
Hardware specifications | laser | Imported; RF CO2 laser; power 100W; power control continuously adjustable; service life more than 30,000 hours |
Scan system | Imported; galvanometer dynamic focusing; focal plane spot size: ≤0.4mm; focal depth: 10mm; ***scanning speed: 5m/s; scanner repeat positioning accuracy ≤0.02mm |
Optical system | Gold-plated reflector, beam expander |
Powder spreading system | Three-cylinder powder spreading system, with a forming working cylinder in the middle and powder feeding cylinders on the left and right |
working cylinder | The working cylinder piston is guided by four guide pillars; storage chamber volume: 120L |
laser cooler | Fully enclosed constant temperature circulation water cooling, cooling capacity: 1500W; rated power: 1.0KW |
heating system | Working cylinder 0~4KW/powder feeding cylinder 0~2KW fuzzy control power adjustable; temperature closed-loop automatic control |
security measures | Automatic shutdown function, automatic shutdown when malfunction occurs, laser safety protection |
Software work platform | Data processing software and equipment control system software | The data processing software and equipment control system software with independent intellectual property rights independently developed by our company have the following unique functions: Ø Basic functions of data processing: three-dimensional visualization, adjusting workpiece position, rotating workpiece, slice preview, automatic/manual support generation; Ø The slicing function can handle very large-scale models; Ø Spot compensation algorithm with strong error correction function: Ø A variety of scanning methods can improve the molding efficiency while reducing warpage deformation, effectively eliminating the shrinkage internal stress of the molded parts, improving the uniformity of the temperature field, thereby effectively suppressing the shrinkage deformation of the molded parts. Ø Open core forming process parameters: Each parameter (such as laser power, scanning speed, overlap rate, etc.) can be quickly set and controlled individually (customized version); Ø Self-developed software has free lifetime upgrades. |
working environment | Voltage | 3-phase 5-wire, 380V±10% |
frequency | 50Hz±2% |
ambient temperature | 18~25℃ |
Appearance size | 2270mm*1280mm*2080mm (non-operating area) |
4. Equipment list
serial number | name | unit | quantity |
1 | Clearance platform | tower | 1 |
2 | Vibrating screen | tower | 1 |
3 | dust collector | tower | 1 |
4 | Part pallet | set | 1 |
5 | Vacuum cleaner | tower | 1 |
6 | Drying box | tower | 1 |
5. Application cases of honor3d C series products
1) Semiconductor field
2) Medical and chemical industry
3) Mechanical equipment field
4) High-end equipment field
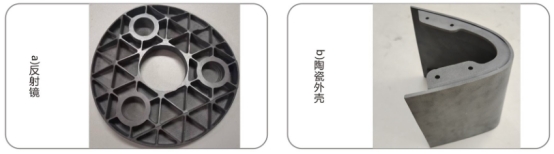