The aerospace industry has widely embraced additive manufacturing technology. This innovation not only simplifies the design process and gives products superior functionality, but also significantly improves production efficiency and promotes the manufacturing of lightweight components. In the industry, diversified additive manufacturing technologies such as selective laser melting (SLM), electron beam melting, binder jetting and direct energy deposition are widely used. These technologies use titanium alloys, stainless steel, aluminum alloys, nickel Materials such as base alloys and cobalt-chromium alloys have been successfully used in the aerospace industry through structural optimization, including civil aircraft and rocket engines, cooling structures, combustion chambers, brackets and countless other key components.
It is particularly worth mentioning that with the progress of design-oriented additive manufacturing (DfAM) in lattice structure design , its application scope has been unprecedentedly expanded in the aerospace field. With its high strength-to-weight ratio, high stiffness and unlimited design flexibility, lattice structures have brought unprecedented performance advantages and application potential to the aerospace industry. For example, researchers used SLM technology to successfully manufacture 316L stainless steel helicopter parts with an internal integrated lattice structure, achieving a weight reduction of up to 50% compared to traditional parts. This breakthrough marks a new milestone in lightweight design.
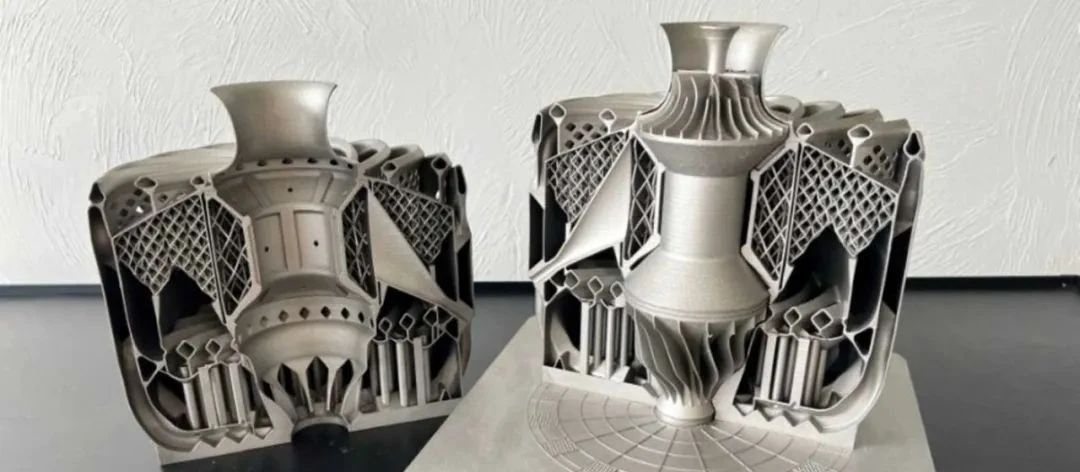
International cooperation projects also demonstrate the great value of additive manufacturing technology. For example, Safran teamed up with SLM Solutions to use SLM technology to produce large nose landing gear parts, significantly optimizing component performance and reliability. The Korea Aerospace Research Institute achieved the dual goals of weight reduction and efficiency improvement through lattice modification of the landing gear.
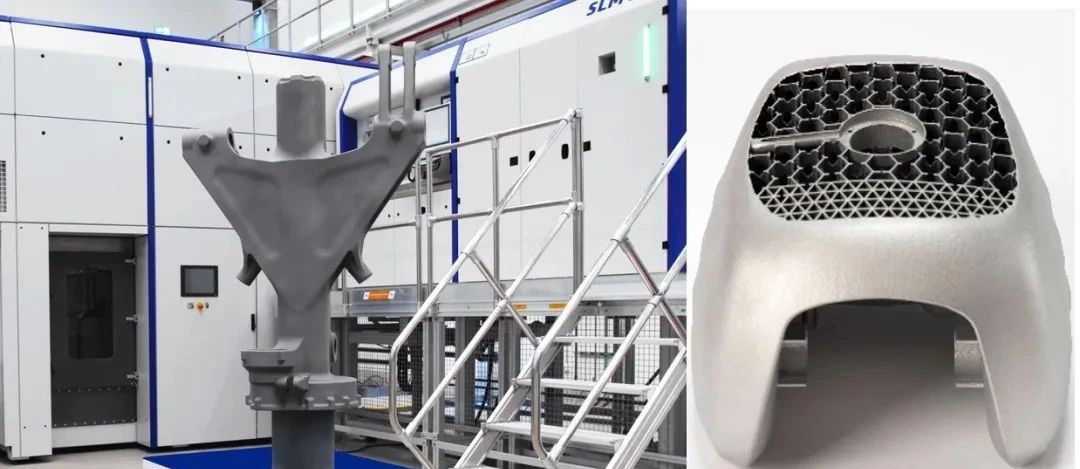
Previous Rocketdyne engineers cleverly used shell and filled grid technology to design a revolutionary Reaction Control System (RCS) four-thrust thruster, which is 67% lighter and 66% cheaper than competing products on the market. It demonstrates the extraordinary ability of additive manufacturing technology in improving product competitiveness. nTop engineers relied on the TPMS lattice structure design to develop an air-cooled heat exchanger that is 85% smaller in size and significantly reduces the number of parts, providing innovative solutions for aerospace thermal management.
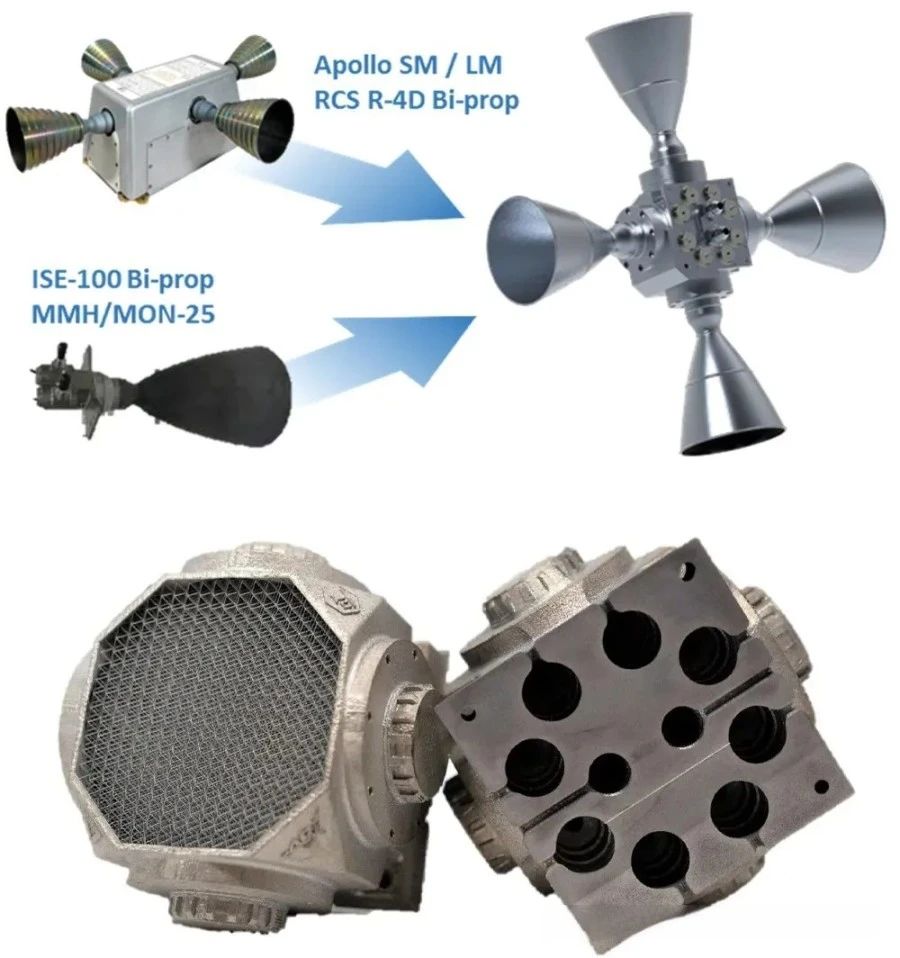
In addition, Cobra Aero optimized the additive manufacturing of the air-cooled cylinder of the drone engine. Through conformal lattice structure design, it not only reduced 50% of material waste, but also demonstrated the advantages of additive manufacturing technology in component integration and performance improvement. Unique advantages. In the research of Mert et al., the lattice optimization strategy was successfully applied to passenger aircraft brackets. Through a series of tests and comparisons of lattice structures, the octagonal lattice structure showed a weight reduction effect of up to 53.8%. Cubic lattice and octahedron The lattice structure also achieved weight reductions of 49.5% and 34.4% respectively, fully verifying the huge potential of the lattice structure in lightweight design.
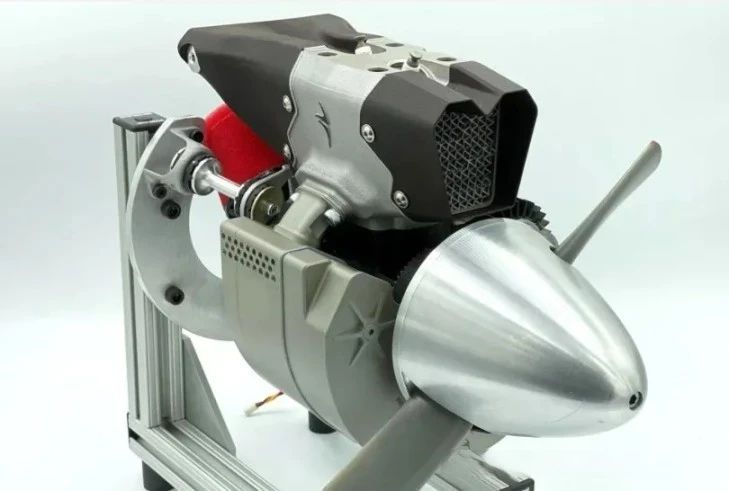
Pioneering research by Doodi et al. introduced an innovative hybrid lattice structure inspired by the overlapping patterns of bamboo and fish scales in nature. By finely adjusting the cell wall thickness, they not only optimized the lightweight properties of the structure, but also achieved excellent compression performance in the aerospace field. On this basis, the author's team further developed a cutting-edge inverse optimization framework specifically designed for the design of high-end aerospace sandwich panels. The framework cleverly utilizes honeycomb units for core topology optimization, taking into account structural compliance and thermal management needs.
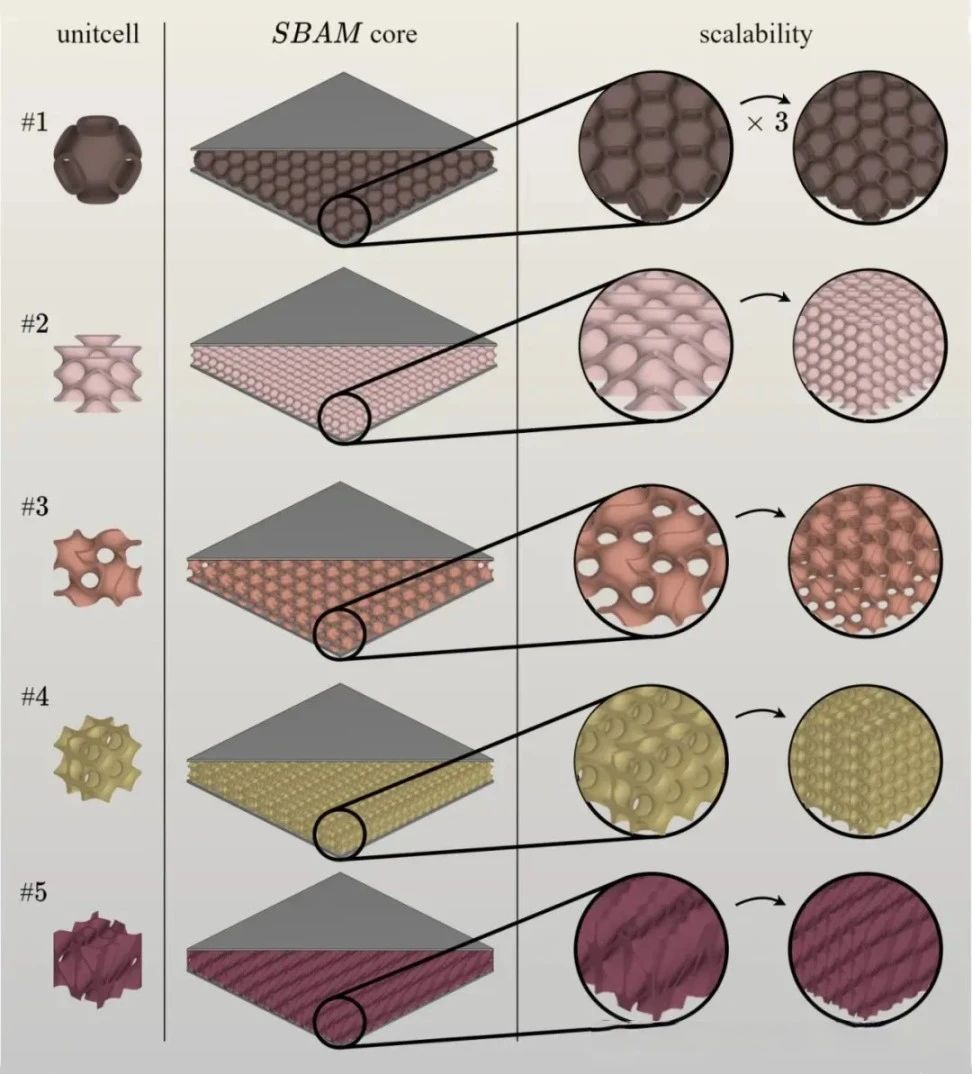
At the same time, a strut-based lattice core sandwich panel design was proposed, tailored for aerospace applications . The design uses a linear elastic frame model to accurately predict the displacement and stress distribution in the structure. By comprehensively considering shear force and normal force, it achieves in-depth optimization and performance leap in the lattice core design. In order to meet the needs of large-scale panels, curved sandwich panels are specially introduced in the design to flexibly connect the lattice core and skin. At the same time, the innovative pin method effectively releases the rotational freedom between adjacent nodes, allowing the adjustment of the lattice core unit. The size or number becomes simpler, thereby significantly improving the mechanical properties of the curved lattice structure.
In the aerospace industry, sandwich structures are invaluable in achieving weight reduction goals. The study delved into the impact of core size, shape and orientation on panel structural dynamics and showed that the zero-degree hexagonal core achieves an ideal balance between stiffness and damping properties. In addition, in response to the urgent need for aircraft engine noise control, researchers innovatively proposed an acoustic sandwich structure using additive manufacturing sound absorbers. Compared with traditional perforated honeycomb cores, this new structure has better sound absorption under the same mass and thickness. The efficiency is increased by 90%, and the bending stiffness is also increased by 10%.
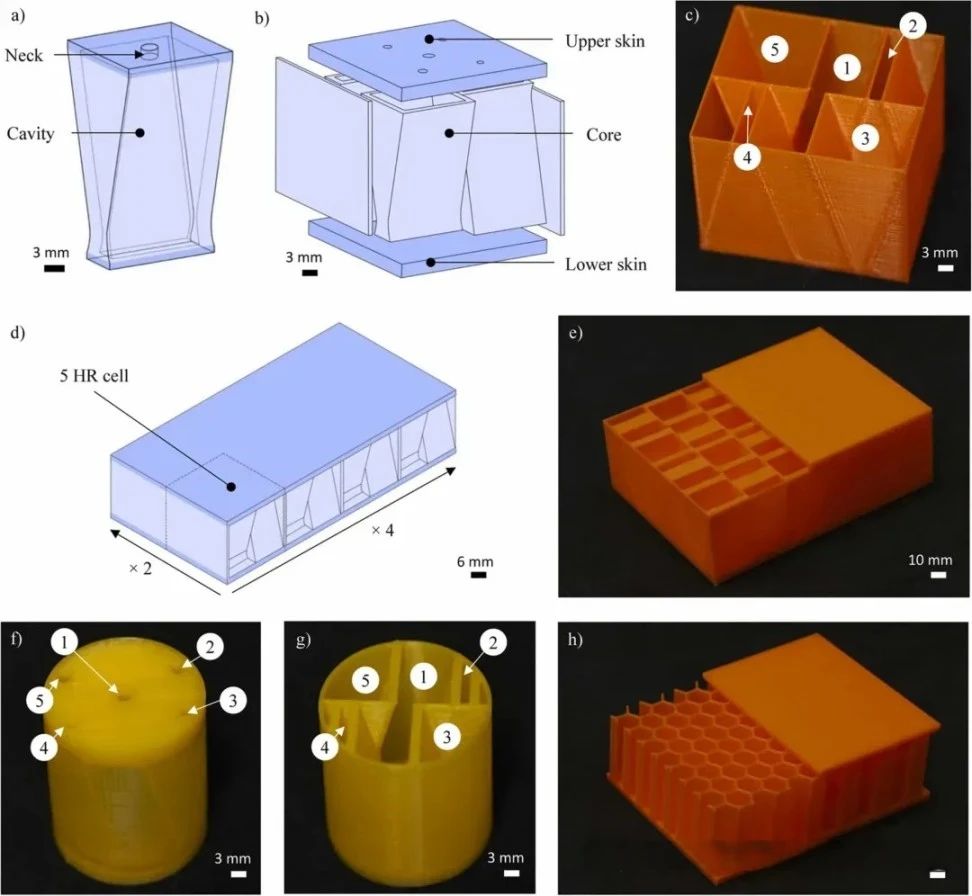
In the process of exploring new paths for the design of aerospace sandwich panels, researchers from the Zhejiang Provincial Key Laboratory of Robotics and Intelligent Manufacturing Equipment Technology came up with a unique approach , combining the laying strategies of continuous long fibers and composite short fibers , using continuous and lattice arrangements respectively to achieve It significantly improves the mechanical properties of fiber-reinforced polymers in matrix composite materials, effectively reduces weight and optimizes material utilization. At the same time, research on the crashworthiness of aerospace components has also made breakthrough progress. By comparing 11 different lattice structures of thin-walled honeycomb or metal foam structures, the superiority of the octagonal lattice structure in crashworthiness was determined. . After topology optimization, the twisted octagonal lattice structure stands out and achieves high specific energy absorption capacity with its relative density of only 20%.
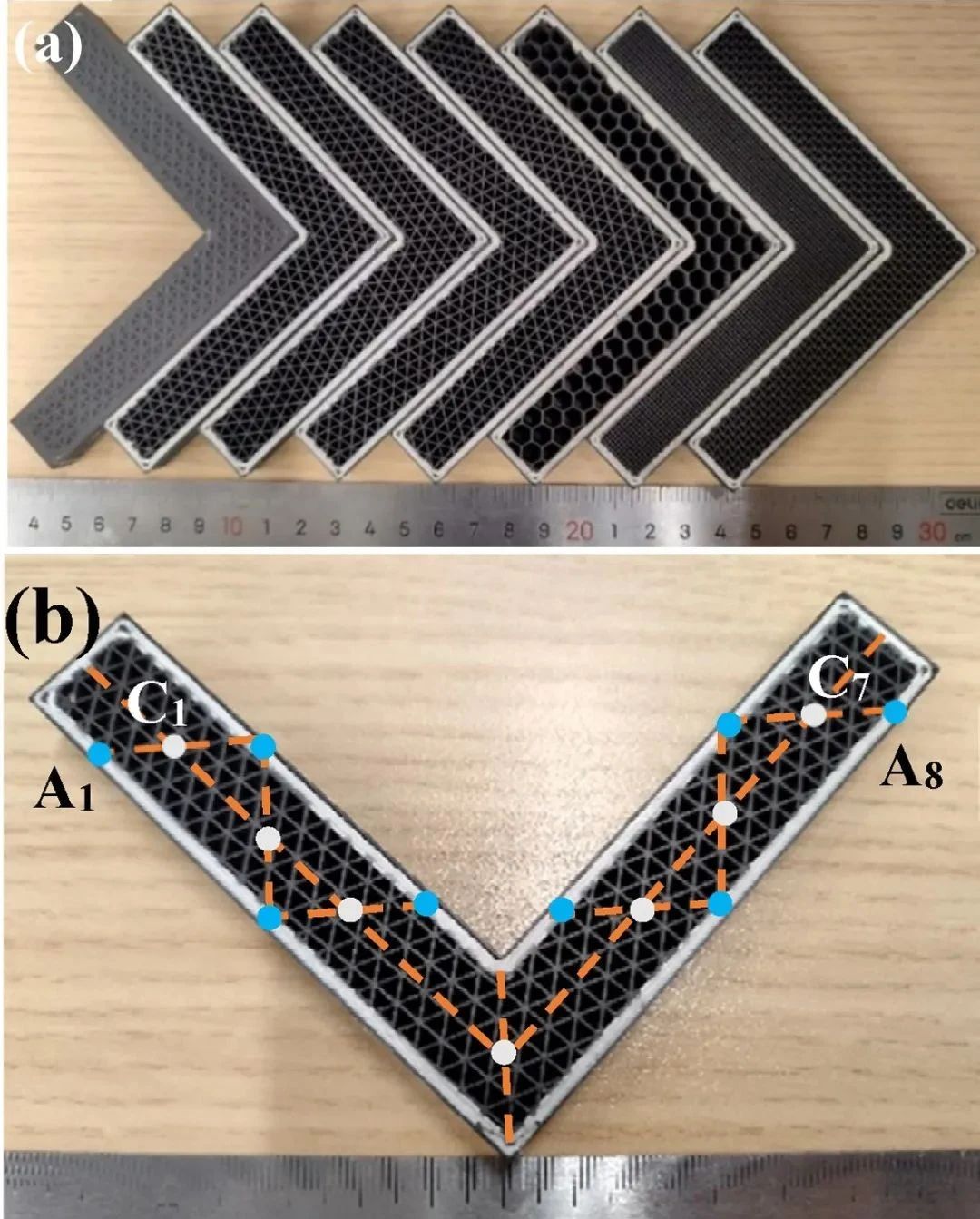
In the field of aircraft wing design, the application of lattice structures is also eye-catching. Several studies have shown that incorporating lattice structures into different components of the wing can significantly reduce weight by up to 30%. The research by Spadoni et al. further revealed the potential of chiral lattice structures in aircraft wings, demonstrating their extraordinary ability to withstand significant deformation without exceeding yield strain. The truss-based 3D lattice structure proposed by Magna Parva provides a new solution for the return capsule landing buffer system, demonstrating the application value of the lattice structure under extreme conditions. The work of Moon et al. focuses on the lattice design of deployable drone wings. Through the exploration of three different structures, the flexibility and elasticity of the wings are maximized.
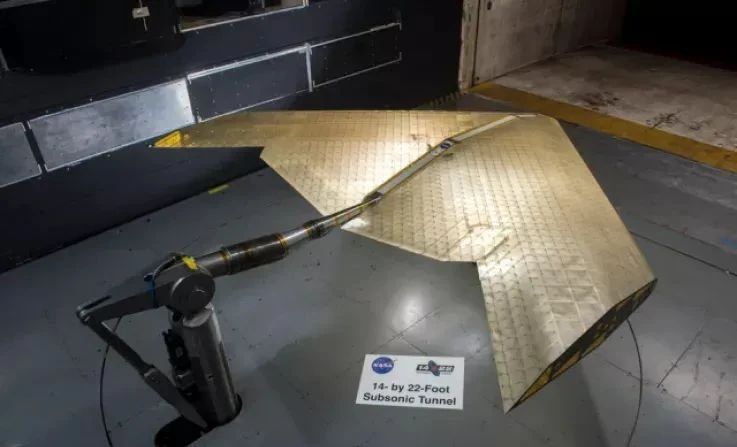
Facing the future, programmable material systems and active deformation technology have brought unprecedented changes to the aerospace field. Through the subtle use of lattice structure design, these systems can not only realize the construction of adaptive structures and mechanisms, but also exhibit excellent elasticity and shape deformation capabilities under external loads. The success of the full-scale wind tunnel test verified the huge potential of these technologies in improving aerodynamic efficiency and roll control certainty. In addition, active morphing wing technology is gradually becoming a reality with its advantages of low density, spatial adjustment rigidity and high compliance structure, bringing a double leap to the aerodynamic performance and production efficiency of the aircraft.
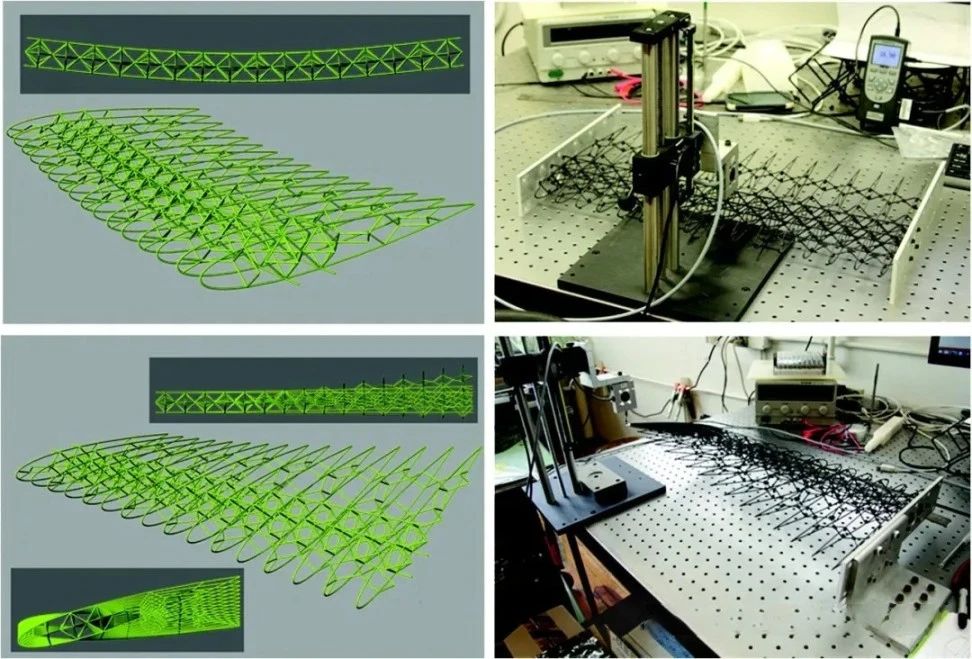
Of particular note is the concept of active 3D printed lattice structures, which can achieve shape changes based on temperature and displacement control conditions, providing an unprecedented degree of freedom for aircraft design. Through the application of gradient frame design and non-uniform density method, the new morphing wing structure not only achieves significant weight reduction (about 36%), but also greatly improves torsional performance (more than 50%). These developments not only broaden the design boundaries, but also open up new paths for the development of ultra-light deformable components.
Although lattice structures are widely used in the aerospace field, the aviation industry still faces major challenges such as rising fuel costs, carbon tax pressure and exacerbating global warming in the pursuit of green aviation and sustainable development. Green aviation aims to improve the industry's environmental sustainability by reducing greenhouse gas emissions, optimizing fuel use and promoting comprehensive environmental protection of aircraft operations and technology. Although traditional methods have made contributions, their efficiency improvements are limited. Future hopes are pinned on modern aircraft designs, such as SAW Revo, Zephyr drones and Airbus 2050 concept aircraft, which demonstrate technologies such as ultra-light structures, solar energy utilization and bionic design.