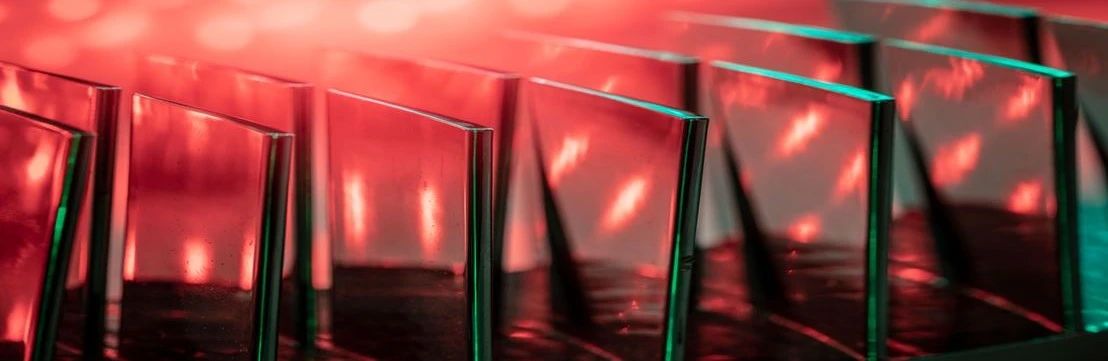
Post-processing , especially surface finishing, currently remains one of the main challenges of additive manufacturing. Surfaces have a strong influence on mechanical properties such as part fatigue and functionality. When parts are taken out of the powder bed after printing, they are rarely used directly as final products.
There are now a wide variety of surface treatments available, and the number is growing all the time. How to choose the right processing method and when to do it can open up many new opportunities for additively manufactured parts.
Before considering different finishing techniques, you need to know what kind of surface quality you can achieve on your additively manufactured parts.
Working with the head of the additive manufacturing department at the Technical University of Freiburg in Germany, we used three different methods for surface post-processing and analyzed the surface roughness at different printing angles:
· Sandblasting
· Centrifugal grinding
· Plasma electrolytic polishing
The state of the surface after printing and the impact of surface finishing were first evaluated on a small test sample (printed on EOS M 290 using EOS StainlessSteel 316L), and finally applied to actual application parts.
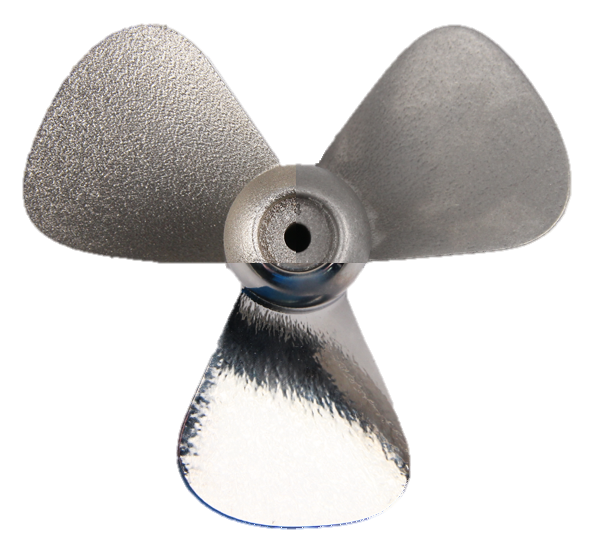
What kind of surface roughness can be expected after 3D printing ?
Depending on the printing angle, different surface qualities will be obtained. Analysis of 316L parts shows that the average roughness (Ra) that can be expected after printing can be between 5 and 45 µm. The difference between the upper and lower surfaces can be clearly seen.
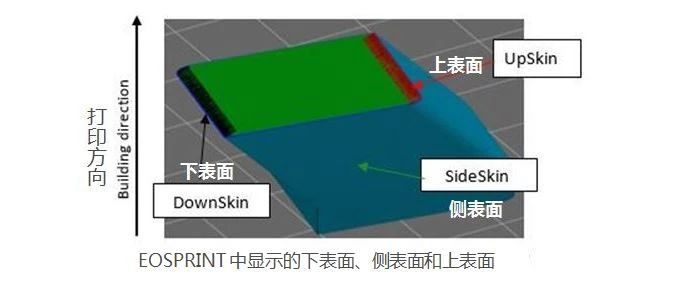
There are many reasons for differences in surface quality. One of the major influencing factors is the type of exposure strategy used for a specific area. For these parts, side surfaces, upper surfaces, and lower surfaces can be clearly distinguished.
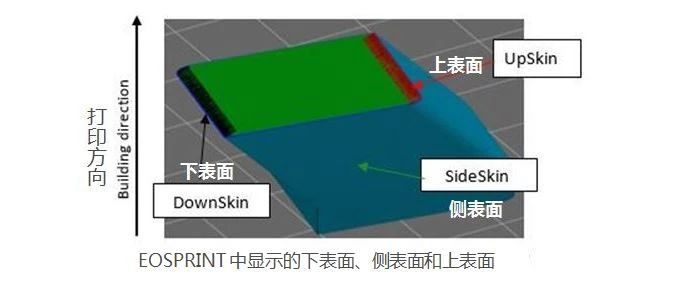
Even though upward-facing surfaces generally have better surface quality than downward-facing surfaces, especially flat upper surfaces usually exhibit higher roughness values due to the step effect and molten particles on the surface.
The same is almost true for the lower surface area, as the superimposed material melts at the surface and there is less material locally to conduct heat energy, which results in higher roughness.
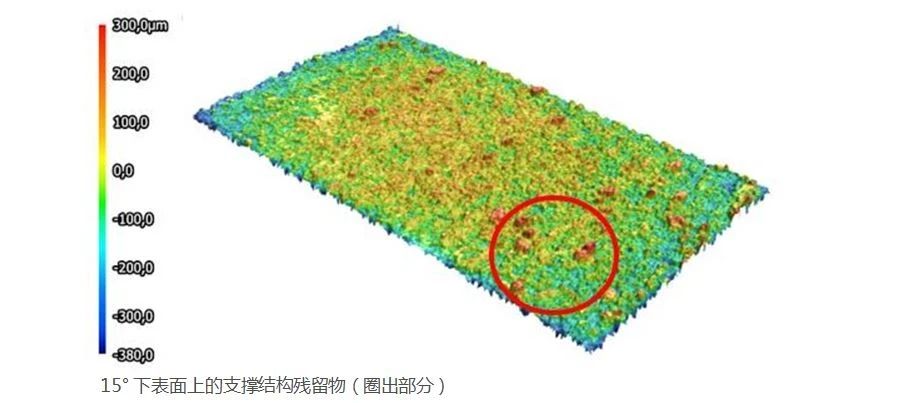
For certain small angles, supports are often used to improve heat transfer and buildability, and to avoid part deformation. Supports need to be removed and often result in higher surface roughness as residues of the support structure remain on the surface. This particle, as well as the melted particles, will protrude from the part surface to 200-500µm, which will greatly increase the surface roughness.
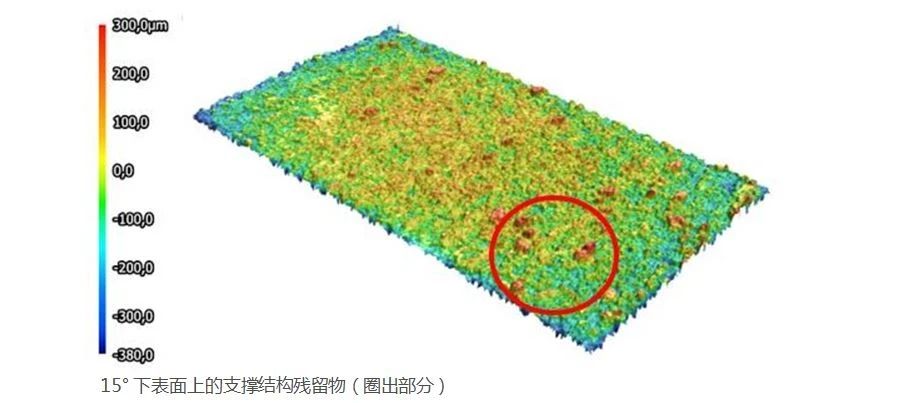
The results show that the overall surface quality of the part can be very uneven. Non-uniformity of the surface can increase the difficulty of finishing later on, and an already smoother surface (such as the upper surface) can be finished to the desired condition more quickly than a rougher surface (such as the lower surface and the surface of the support area).
This often requires a more selective approach to the surface finishing process, or an intelligent combination of different finishing methods.
How to effectively reduce surface roughness?
Sandblasting is one of the first surface preparation steps for 3D printed parts. Typically, sandblasting is used to remove residual powder particles from a surface, smooth the surface, or change the appearance of a part. In some aspects, the sandblasting step can be used as an initial step to homogenize the surface of a part to reduce the difference in roughness between the lower and upper surfaces.
There are many different media available for sandblasting, varying in shapes, sizes and materials. In this study, commonly used blasting media were used:
Nutshell
glass beads
silicon carbide
ceramics
Surface roughness after sandblasting
The results after sandblasting may vary depending on the blasting media used, compare below:
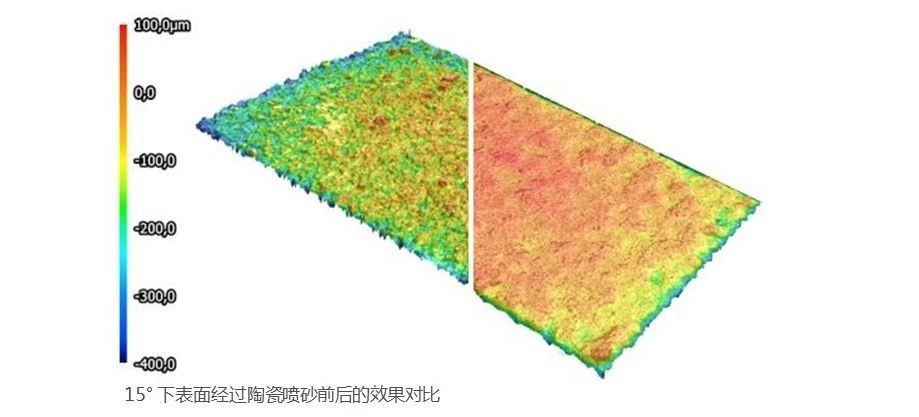
With the exception of Nutshell, the blasting media used can reduce the top and side surface roughness by 30% to 65%. The effect is more pronounced on the lower surface and support areas. Taking ceramics as an example, the lower surface roughness is reduced by nearly 80% even at the support angle.
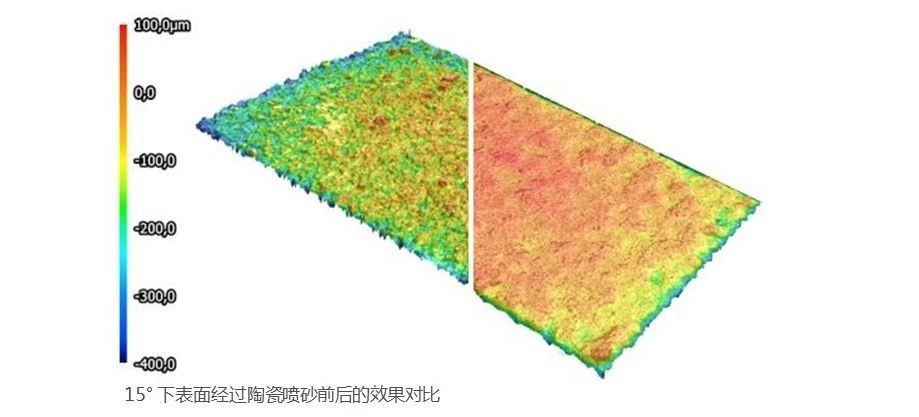
Using sandblasting as an initial finishing step can already reduce much of the roughness, especially in the lower surface areas. Therefore, it is also an essential first step for other surface treatments.
This process is widely used for polishing metal parts and can be used for a variety of purposes, such as deburring, grinding or polishing. The media for centrifugal grinding typically vary in material, shape, and size, and are often combined in a multi-step process. In this study, a single-step grinding media was used to rapidly reduce roughness.
With centrifugal grinding, roughnesses of Ra <1 µm can usually be easily achieved on upward or vertical surfaces, but in the lower surface area the process can take quite a while to remove all lower surfaces or residues on the support structure.
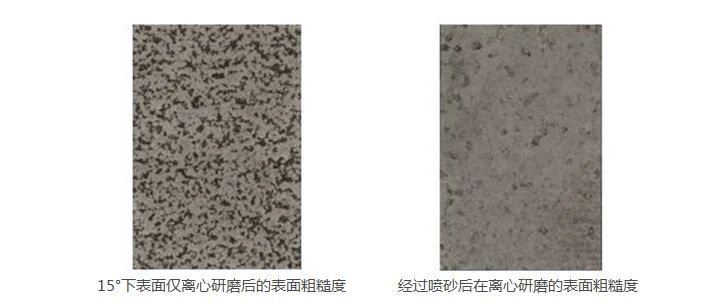
For example, the normal lower surface area can reach values of Ra <4 µm after 180 minutes of treatment, while the surface in the support area is still significantly rougher. To close the gap between the best and worst surfaces, sandblasting can be performed beforehand for a more uniform finish.
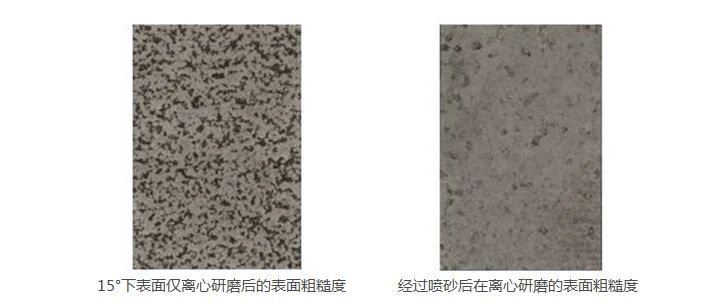
Sandblasting has removed some of the raised surfaces and resulted in a more uniform surface, so less material is removed by centrifugal grinding, saving time and getting better results.
The third finishing process - plasma electropolishing (PeP). This is an electrochemical process that removes material through a combination of different chemical reactions within a plasma layer formed on the surface of the part. Compared with traditional electrochemical polishing, this process uses water and special salts as electrolytes instead of acids.
Plasma polishing produces an extremely smooth and clean surface, making it ideal as an excellent finishing step.
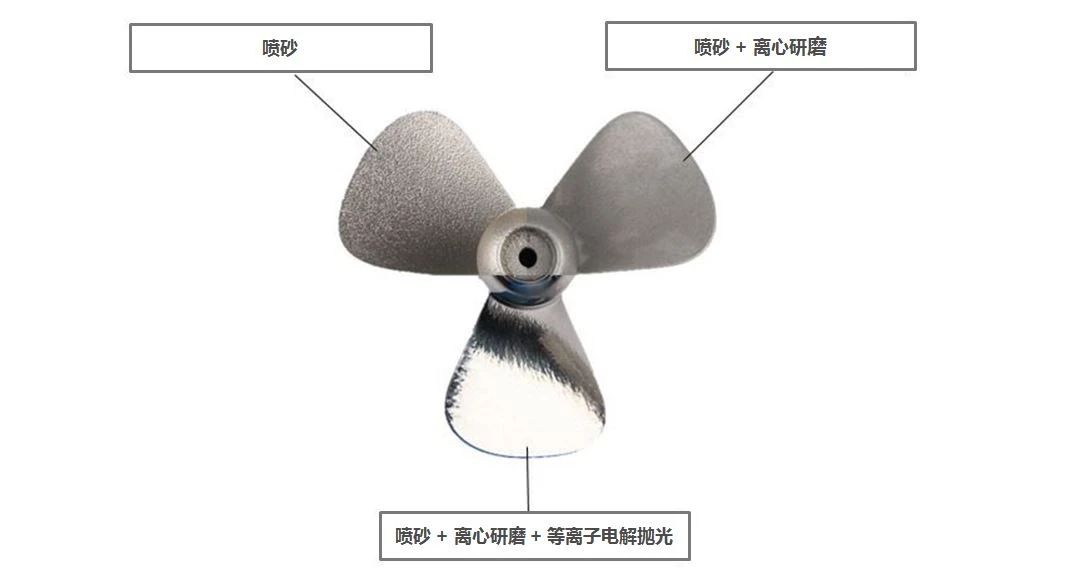
Similar to what was mentioned before, a very good surface finish can be achieved with plasma polishing alone, but it may take some time to remove all the underlying surface roughness on its own. To speed up the process, sandblasting can again be used as a first step. This reduces the processing time of the lower surface area to just a few minutes, achieving Ra <4 µm even on supported lower surfaces.
This process does not have to be combined with sandblasting only. It can also be used as a final finishing step on centrifugally ground parts, achieving a nice glossy finish in minutes. If all three steps are combined, the surface roughness can be reduced to Ra <1 µm even in the lower surface area.
Finishing of complex parts
Since the previously mentioned results may vary depending on the geometry, these techniques need to be equally applicable to more complex parts. For this purpose, small propellers printed in 316L can be found in industrial, maritime or oil and gas applications. The surface finish requirement for this part is Ra <3.2 µm.
If you now combine the advantages of these three processes and apply them to a propeller:
Sandblasting – more uniform surface quality
Centrifugal grinding – removes rough projections
Plasma Electropolishing (PeP) – for clean and smooth surfaces
After a total treatment time of 4 hours, the overall surface roughness on the upper and lower surfaces was Ra = 1-3 µm.
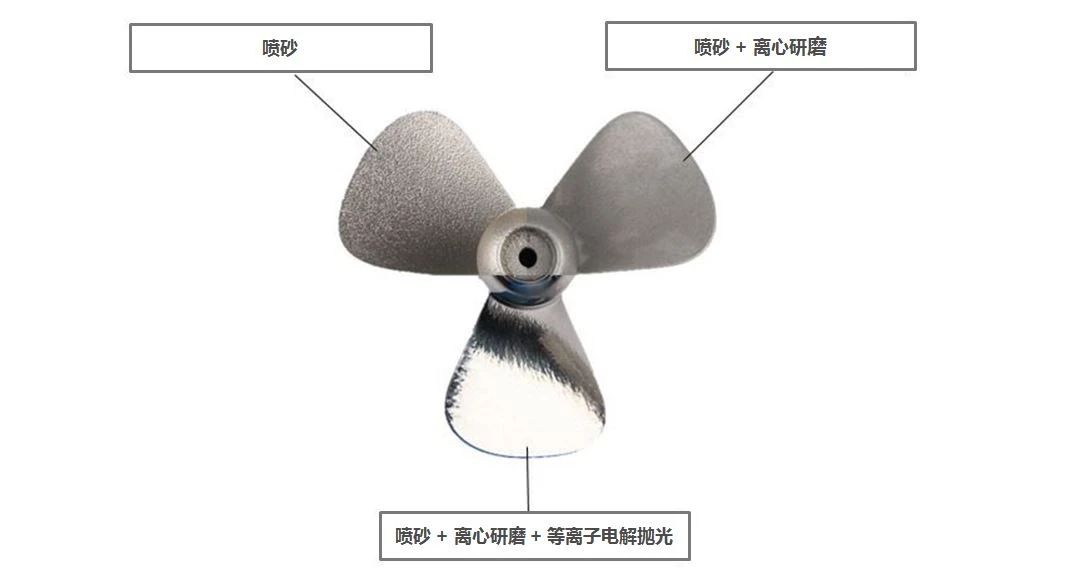
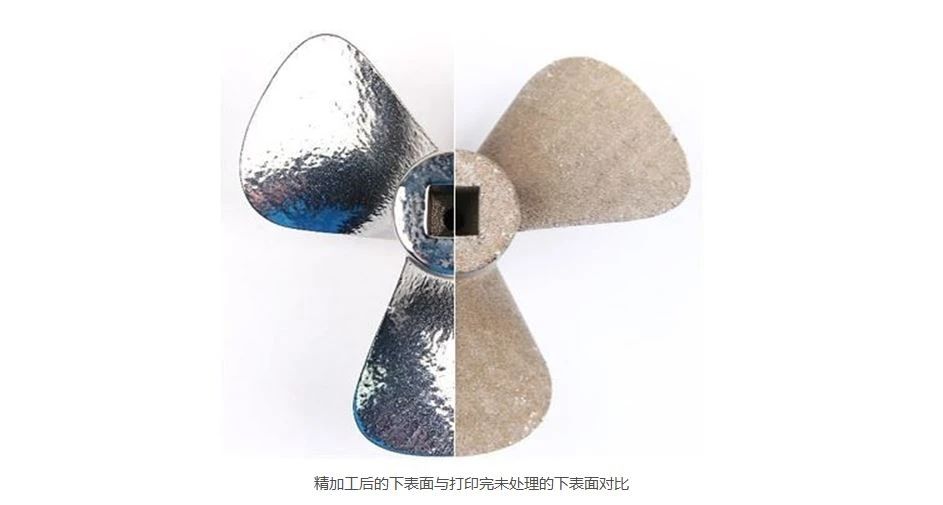
Surface quality and appearance will vary depending on the angle of 3D printing. To obtain the best results, one needs to understand the changes in initial surface quality and the differences between surface treatment technologies.
This study shows that the sandblasting process has great potential as a first step to reduce roughness variations at different printing angles, especially selectively in the lower surface area, where roughness can be reduced by up to 80%. . By centrifugal grinding and plasma electropolishing, the surface can be treated to values less than Ra = 1 µm with good gloss.
However, in most cases, no single solution can achieve the ultimate surface treatment of complex parts. Great results can be achieved through an intelligent combination of different treatments.