The fourth industrial revolution, also known as Industry 4.0, follows the steam technology revolution (the first industrial revolution), the electric power technology revolution (the second industrial revolution), and the computer and information technology revolution (the third industrial revolution). Another major technological revolution followed. Its core features include the use of advanced technologies such as artificial intelligence, big data, the Internet of Things, and cloud computing to realize the intelligent, networked, and service-oriented transformation of the manufacturing industry. This revolution not only profoundly changed the way of production, but also greatly improved production efficiency and product quality, and promoted the optimization and upgrading of the global economic structure. Additive manufacturing technology is an important part of the fourth industrial revolution. Combined with core technologies such as artificial intelligence, big data, and the Internet of Things, this new manufacturing method has triggered revolutionary changes in the manufacturing industry. Therefore, additive manufacturing technology has become the focus of competition among powerful countries at the forefront of science and technology.
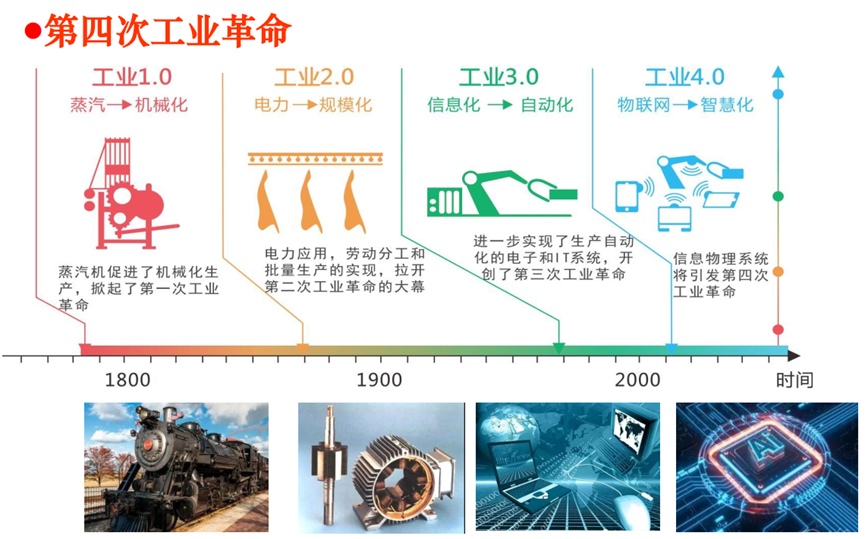
Figure 1 The beginning and technological focus of the Fourth Industrial Revolution
1. Accelerate product research and development to achieve innovation, lower the threshold of manufacturing and promote entrepreneurship
In the traditional product development and design process, there will be a series of long cycles from thinking about design, sample manufacturing, testing and evaluation to final design plan and process determination. In the entire new product development cycle, sample trial production takes 50-80% of the time and cost. Additive manufacturing technology can quickly transform designs into physical prototypes, greatly shortening the time required for traditional prototyping. This enables companies to evaluate and verify multiple design options in a short period of time to quickly determine the final solution.
The Biden administration has proposed that "90% of companies can reduce material costs by 90% and reduce energy consumption by half through 3D printing technology, which is conducive to reducing costs." Not only that, companies can also quickly carry out 3D printing technology during product development. Iterate and respond quickly to market changes and customer needs. Designers can quickly modify designs and reprint prototypes based on user feedback, thus speeding up the process of product optimization and improvement.

Figure 2 Additive manufacturing can save a lot of time and cost in prototype trial production
The production process of the traditional manufacturing industry is a complex and systematic process. The manufacturing of a product may require multiple processes, starting from the initial ingot casting, which may undergo multiple cold processes such as rolling, forging, and drawing. , as well as multiple different processes such as turning, milling, grinding and other mechanical processing to ensure accuracy and surface smoothness. Therefore, the traditional manufacturing model is an interrelated and interactive system. Close cooperation and coordination are required between all links to ensure the smooth progress of production activities and the stable improvement of product quality. Therefore, for traditional manufacturing companies, they need to have multiple workshops and multiple equipment to undertake the processing tasks of different processes in order to obtain the final product.
The emergence of additive manufacturing has transformed product processing from multiple workshops to one additive equipment, and the start-up capital has also been reduced from tens of millions of dollars for several types of equipment to millions of dollars for one piece of equipment. In addition, the high automation of additive equipment will also drive the development of entrepreneurship from professional to popular. From the customer's perspective, products will also be improved from mass-produced standard products to differentiated products that are personalized and customized according to different needs. All the above factors provide new opportunities for entrepreneurship.

Figure 3 Additive manufacturing technology promotes enterprise manufacturing from multiple workshops and multiple equipment to one equipment, lowering the threshold for starting a business
2. Development direction and challenges of additive manufacturing technology
From the perspective of the development history of manufacturing technology, humans mastered equal material manufacturing technology (casting, forging, welding, etc.) more than 3,000 years ago, and subtractive manufacturing technology was developed with the advancement of materials more than 300 years ago. In the past century, the gradual development and integration of digitalization and manufacturing technology have brought new opportunities, and a new manufacturing technology has emerged, which is additive manufacturing technology.

Figure 4. Additive manufacturing has developed from the original point forming to different methods such as surface forming and body forming.
After the concept of additive manufacturing was proposed, new technologies and new principles continued to emerge through unremitting research by domestic and foreign scholars. Additive manufacturing has gradually developed from point-by-point forming to surface forming and even volume forming. Its high degree of freedom and flexible design promotes the further improvement of functional and structural integration, and promotes the development of interdisciplinary and various new industries. It also provides new ways for design innovation in various industries. For example, a certain model of engine can take advantage of the integration advantages of additive manufacturing to integrate more than 20 parts into one, while reducing weight by 25% and increasing work efficiency by 15%. Motorola uses 3D printing technology to produce customized mobile phone cases. While new technologies bring changes and innovations to the industry, they also pose new challenges to the training of talents in related disciplines.
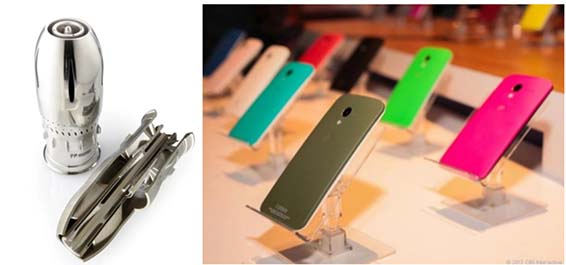
Figure 5 Integrated engine and personalized mobile phone casing
3. Major changes in product design and manufacturing models
The development of additive manufacturing technology has promoted the application of forward design thinking. Forward design is guided by the functional requirements of the product and reduces costs and improves performance through optimized design. Because additive manufacturing is not restricted by traditional manufacturing processes, it provides technical support for forward design, allowing designers to more freely exert their creativity, create products with disruptive designs, and explore new design fields and application scenarios. The design changes brought about by additive manufacturing are multifaceted and far-reaching. It not only improves the degree of design freedom, accelerates design iteration, and transforms design thinking, but also expands the design ecology and innovates design services. These changes have injected new vitality and impetus into the development of industrial design and manufacturing.
The application of additive manufacturing in the biomedical field has also received widespread attention, playing a leading role in the future development of medical technology. For our country, under the premise that people's life and health have become a major demand for a well-off society, more than 90% of high-end medical devices in our country still rely on imports. The resulting high consumption has caused many people to return to poverty due to illness, causing serious national problems. and social problems. The application of additive manufacturing in medicine initially evolved from assisted manufacturing of medical models and various instruments to the manufacturing of various prosthetic substitutes and regenerative scaffolds. In the 21st century, with the improvement of 3D printing technology, it is now possible to print active tissues. For example, 3D printing of functionalized active myocardial patches is mainly aimed at myocardial infarction, a disease that seriously threatens people's lives and health. More than 500,000 patients in my country are threatened by myocardial infarction every year, and the need is very urgent. Using 3D printing technology to create a suitable active myocardial patch and implant it can promote regeneration of the infarct area and repair the function of the heart. Among them, multi-scale biofiber/active cell composite printing and achieving beating ability have become the difficulties and challenges of this technology.

Figure 6 Schematic diagram of the structure and implantation of active myocardial patch
Finally, through the development of a high-precision, multi-nozzle active tissue 3D printing system, we successfully printed active myocardial patch materials with fiber line widths of 0.2-10 microns and cell activity >95%. Through implantation, it can effectively promote the regeneration of infarcted myocardial tissue and open up new ways for the treatment of patients with severe myocardial infarction.

Figure 7 Comparison of active myocardial patch repair strategy and effects before and after repair
Additive manufacturing technology (3D printing technology) has now become a tool and weapon for innovation and entrepreneurship, and it is also a cutting-edge technology in the scientific and technological competition among the world's powerful countries. At present, this technology has achieved remarkable industrial results, has had a major impact on all walks of life, and will also bring about major changes in the model of future industrial society. The development of this technology has also put forward new requirements for the education industry and disciplines, and the goal should be to cultivate new engineering integration talents. If you want to continue to promote the development and application of additive manufacturing, an emerging technology, you not only need to inspire unbridled ideas, but also need to be down-to-earth and brave to explore.