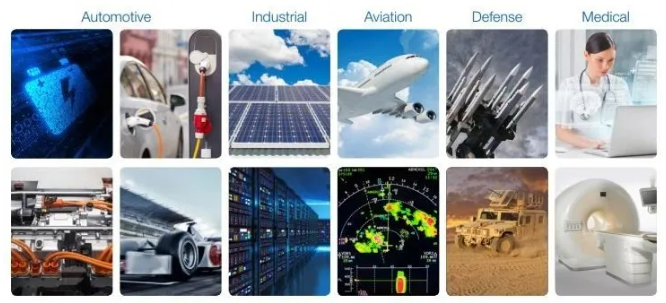
Wide application of silicon carbide ceramics
Currently, the demand for SiC ceramics with various complex structures and shapes has increased dramatically. Traditional manufacturing methods are complex, time-consuming, and have long mold design and production cycles. Due to its extremely high hardness and brittleness, it is extremely difficult to process. Not only are the tools severely worn, but they may also produce defects such as cracks, making it difficult to achieve good surface quality and dimensional accuracy. Based on the above shortcomings, SiC ceramic preparation technology combined with 3D printing technology has become the main development direction of current research and application. It can well solve the problems of traditional ceramic materials with complex shapes that are difficult to form and process, long production cycle, and high cost.
Currently, the technical types of ceramics produced by 3D printing mainly include SLS (laser powder sintering), DIW (direct ink writing), SLA (light curing), BJ (binder jetting) and FDM (melt extrusion). Shanghai Silicon Researchers from the Institute of Salt and Chemical Research have tested and certified these ceramic 3D printing technologies.
Unlike metal 3D printing, ceramic materials cannot be directly printed by heating ceramic powder with a laser. The thermal stress generated during the sintering process of direct SLS parts is difficult to avoid cracks, resulting in poor mechanical properties of the final product.
Direct ink writing (DIW) technology is to mix ceramic powder with various organic substances to make ceramic ink, and then print it on a forming plane through a printer to form a ceramic body. Currently, the difficulty with this technology is that the solid content in the ink is too low, which results in a low density ceramic body.
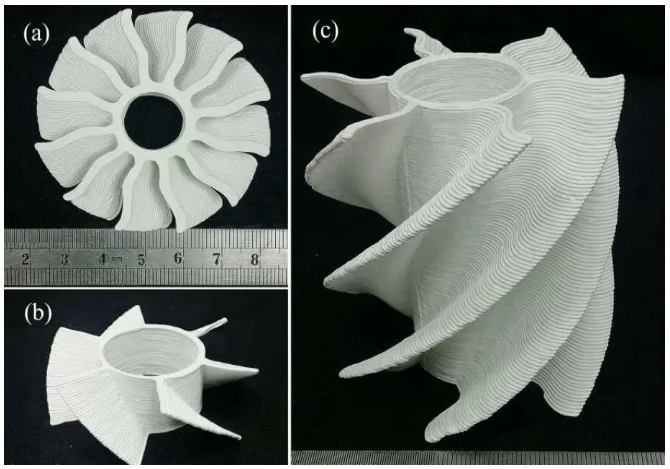
Al2O3 body 3D printed using direct ink writing technology
SLA is an effective UV curing technology based on photopolymerization of photosensitive ceramic slurry. It is the current mainstream ceramic 3D printing process. However, due to the high absorbance and high refractive index of silicon carbide, the cured thickness and solid content of the slurry are limited. parameter.
Powder fused deposition modeling (FDM) 3D printing technology is based on the traditional fused deposition method, using powder mixing and then extrusion mechanism 3D printing to prepare SiC ceramics. This method has the following advantages: it can be printed with powder and the raw materials are conveniently prepared; At normal temperature, the adhesive has strong bonding force; at high temperature, the adhesive has good fluidity; stress can be eliminated through temperature control during the printing process; printed samples have high strength at normal temperature; printed products can be sintered at normal pressure SiC ceramics are prepared by preparation or reaction sintering; the printing material can be recycled.
The BJ process can quickly print complex shapes while maintaining printing accuracy. However, the BJ process limits the filling density of the powder, resulting in a limited SiC volume fraction.
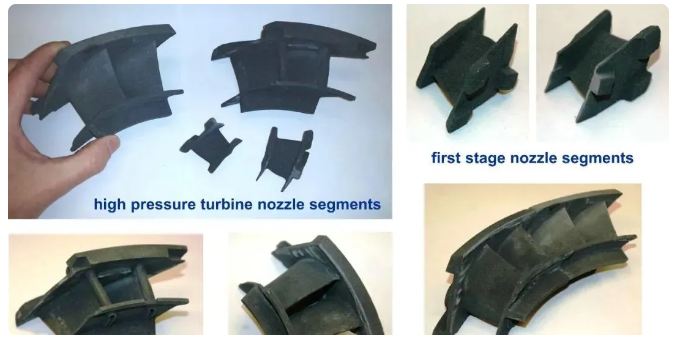
SiC ceramic composite turbine engine parts printed using binder jetting technology at NASA Glenn Research Center
Ceramic materials prepared by conventional 3D printing methods often have high organic content, which is conducive to printing and molding. However, the solid content of ceramics is relatively low. It is difficult for general materials to achieve high density using the normal pressure sintering method, while SiC reactive sintering is through infiltration. The molten silicon reacts with the carbon in the green body and combines the SiC particles in the green body to achieve densification of the ceramic. Compared with conventional methods such as normal pressure sintering and hot press sintering, it is easier to achieve material densification. At the same time, reaction sintering has the characteristics of low sintering temperature and small dimensional change before and after sintering.